Pre-shipment Inspection – The Fundamentals
by: Quest Claire
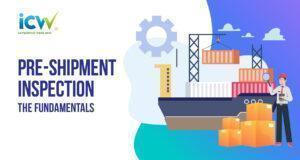
We rely on pre-shipment inspection to assure products meet quality requirements before they are sold to customers. Our QA Manual states that a signed sample should be sent to our contract inspection company for review and use, to represent the quality of the product for inspection. Unfortunately, it may happen, in a rare situation though, that we may not be able to get the sample as it is even not available. When that happens, the inspection takes place without the sample. We must then request the inspection company to inspect without the sample and report as such in the inspection report.
Our QA Manual also specifies a pre-shipment inspection, unless otherwise specified, should be done per AQL 2.5% for major defectives, and AQL 4.0% for minor defectives. We specify ‘zero’ acceptance number for any critical defects. However, we do not explicate the meaning of major, minor, or critical defect. We believe that we can rely on the professional expertise of the inspection company to make such determination as necessary and appropriate.
Moreover, our QA Manual states that there must be 100% product produced and 80% product packed in their pre-shipment forms, for sampling inspection to be conducted. We also expect the contract inspection company to enforce our policy. In fact, I do recall seeing pre-shipment inspections abortive when either the quantity produced, or quantity packed significantly falls short of these specified quantities.
Since I am going to review the subject of ‘Protection against Risks’ on sampling inspection, I want to touch on the following topics as they are so closely related:
- Signed sample as inspection reference
- Conformance to specification and fitness for use
- AQL sampling plans – an introduction
- Classification of defects (defectives)
- Randomness of the sample selected for inspection
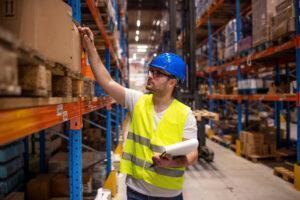
Signed sample as inspection reference
It is obvious to me that product quality falls broadly into two categories: a. aesthetic quality (sensory characteristics) in terms of color, surface finish, size, shape, … etc., all factors that appeal to senses; b. operation and performance quality in terms of operation of its intended function over a reasonable period of time that defines the product designed and manufactured as an equipment. When a signed sample is available for use as a reference, both categories of quality are completely represented by the signed sample.
When a signed sample is absent, I know that inspectors must rely on their experience to create such quality requirements based on their experience from previous inspection on similar products. I understand it is possible that these created quality requirements might not represent the quality requirements in their totality of the buyers, the designer, or the marketing team of our company. Although product specifications sheets and product photos are provided to support the inspection, very likely some of the quality requirements may not be fully and clearly provided to the inspectors.
When an inspection report states that ‘signed sample is not available’, it means that the inspection was not done referencing the quality requirements in their totality. I believe that this is a gap that warrants an immediate action. I must work with the product development manager and the buyer to make sure this gap is filled, and such risk can be eliminated.
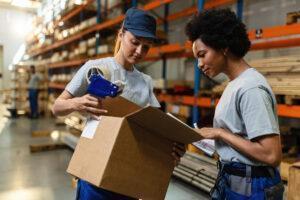
Conformance to specification decision and fitness for use decision
Of all the purposes of inspection, the most ancient and the most extensively used is product acceptance, that is, determining whether a product conforms to
standard and therefore should be accepted.
Product acceptance involves the disposition of product based on its quality or its deviation from the standard. This disposition involves two important decisions:
- Conformance to specification: Judging whether the product conforms to specification
- Fitness for use: Deciding whether nonconforming product is fit for use
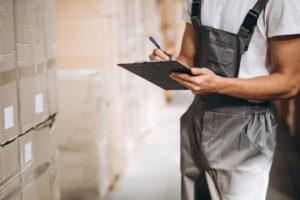
Conformance to specification decision
We picked our contract inspection company based on the evidence that the company is organized so that inspectors can report inspection results themselves. To this end, inspectors are trained to understand the products, the standards, and use of the required inspection and test instruments. They are given the jobs of inspecting and judging conformance. Associated with the conformance decision is the disposition of conforming product. The inspector is only authorized to report inspection results. This decision to “ship” is not made by the inspectors but by me, the QA Manager, on behalf of the management of our company Quality First.
Fitness-for-use decision
In the case of a nonconforming product identified, usually it is my decision to reject shipment. However, under a special situation when I know that the product is highly advertised and must be ready for shipment very soon, though it is rare, I will put the shipment on hold, and I have to ask the question: Does this nonconforming product fit for use or unfit for use? Product features are said to possess “fitness-for-use” if they are able to meet customer demands. Unfortunately, in many cases, the answer as to this question is not obvious. In such cases, a study is made to determine fitness for use. This study involves securing inputs from department representatives of the following: the buyer, the product designer, the product engineer, the marketing team, and myself.
Topics to be discussed usually cover several levels of fitness for use, the safety of the product, the failing to comply with voluntary standards, the marketability requirements, the qualities that determine fitness for the customers, and the qualities that influence field maintenance. The internal costs can be estimated to arrive at an economic optimum. However, the effects can go well beyond money: schedules are disrupted, who should be responsible for the quality problem, … etc.
The job of securing such inputs is often my responsibility to include for example, my quality engineer who contacts the various departments that are able to provide pertinent information. There may be a need to contact the marketing team and even to conduct an actual tryout. Once all the information has been collected and analyzed, the fitness-for- use decision can be made.
In case the fitness-for-use decision favors the shipment to be released, the producer must be notified immediately that the shipment is accepted on deviation, deviated from the established company policy. In case the producer confirms their acknowledgement of the fitness-for-use decision and agrees to bear the potential costs of product return in the future, the producer is then allowed to make shipment. Nevertheless, it is our policy that the producer must review the nonconformance case and present the corrective action plan to prevent future recurrence.
AQL sampling plans – an introduction
Before I want to get started on this big topic, I want to define some terms and clarify their concepts as used in our later discussion.
Basically, sampling inspection is conducted to learn about the quality of a lot of product. The lot, in many cases, is in large quantity. A decision to accept or reject the lot is made from carefully inspecting a small number of units of product, which we define as the sample, drawn from that lot. There are advantages and plausible disadvantage as argued by some people, of inspecting once a single large lot comparing to inspecting a series of small sub-lots splitting from the single large lot. I will have more discussions in the later section as necessary.
Sampling inspection is primarily done for the purpose of lot acceptance for our company as a retailer. However, there are other purposes, and they usually cover determination of product quality, process control, overall QC system audit, overall process capability determination, as duly implemented by the producer.
There are two fundamental concepts required to be defined, respectively inspection by attributes, and inspection by variables.
- Attributes,i.e., the product as a whole is judged in a state of ‘good for use’ or ‘bad for use’, the gaging is on a basis of ‘go’ or ‘no-go’.
- Variables,i.e., certain quality parameters of the product are required to be evaluated along a scale of measurement.
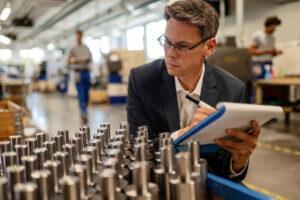
However, in my process improvement plan, inspection by attributes is my only focus at the moment. As far as I understand, inspection by variables may be required when such measurement is deemed necessary in determining the quality of the products.
Since I have been applying sampling inspection method for years, I want to share some discussion on the advantages and disadvantages of this method:
Compared with 100% inspection, sampling has the following advantages for example:
- Economydue to inspecting only part of a lot, sample sizes are only a few percent of the lot quantity, I will provide an example later
- Less-handlingdamage during sampling inspection
- Inspectionjob is less monotonous when comparing lot- by-lot decisions to piece-by-piece decisions
- Lowering the costs of inspection from any destructive testing if such testing is required for determining the quality of the product
- Rejectionson producers of entire lot rather than mere return of the defectives, thereby providing stronger motivation or business pressure to producers for improvement; leading to expected leaps in process capability
Unfortunately, sampling inspections contain some inherent disadvantages for example:
- Thereare risks of accepting bad lots (buyer’s risk), and of rejecting good lots (producer’s risk), even when a random sample is collected. I will have a detailed discussion in the latter section when buyer’s risk and producer’s risk are discussed. Such inherent risks could either increase the quality costs of the buyer or the producer.
- Thesample usually provides less product quality information than what is all there. We know that the sample collected usually represents a very small percentage of the total quantity of the lot, e.g., 4%, considering a sample size of 125 from a lot of 3,125. It should be clear that the product quality obtained from the sample may only represent the little information uncovered from the lot, but much of the information remained hidden.
There are certain criteria required to be fulfilled in using sampling inspection method. The following represents rules for our inspectors to follow:
- The inspector follows the prescribed sampling plan and does not make any deviation from what is prescribed by the sampling plan for acceptance or rejection. This is continuously an area of concern from my part. I keep emphasizing to the contract inspection company that acceptance sampling decision must solely be made based on sampling plans, a statistical decision, and have all psychological judgment to be eliminated.
- The inspection is made without error, i.e., no human or equipment mistakes are made in measurement or in conformance judgment. Inspector error will be detailed in the latter section. This is an area I want to review regularly with the contract inspection company.
- The sample for inspection should be drawn on random base which will be detailed in the following section.
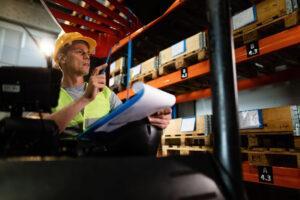
Classification of defects (defectives)
Our sampling plans set up the criteria for judging lot conformance in terms of an allowable number of defectives in the sample. Since defects differ greatly in seriousness, the sampling plans must somehow take these differences into account.
Some quality characteristics and defects are very important to our customers as judged by our marketing team and designers, while others are not. Defective (deviation from the standard) seriousness cannot be judged as easy as it may appear. Inspectors are required to inspect many general consumer products, each of which has different characterizes. Gathering a substantial and sufficient knowledge prior to the inspection of a new product is always challenging, but necessary. From time to time, I reminded our contract inspection company that inspectors should be sensitive to the fact that when an inspection is done on a new product, complete product specifications must be reviewed by the inspectors. Additionally, inspectors must also determine if complete quality characteristic information, though may not be specifically stated in the product specifications, should be grasped prior to an inspection.
We do not define major, minor, or critical defect. We rely on the following general definition as called out from the acceptance sampling standard ANSI/ASQ Z1.4 Sampling Procedures and Tables for Inspection by Attributes, which we follow.
Critical Defect: A critical defect is a defect that judgment and experience indicate is likely to result in hazardous or unsafe conditions for individuals using, maintaining, or depending upon the product.
Major Defect: A major defect is a defect, other than critical, that is likely to result in failure, or to reduce materially the usability of the unit of product of its intended purpose.
Minor Defect: A minor defect is a defect that is not likely to reduce materially the usability of the unit of product for its intended purpose, or is a departure from established standards having little bearing on the effective use or operation of the unit.
We do not define major, minor, or critical defective differently. We rely on the following general definition as called out from the acceptance sampling standard ANSI/ASQ Z1.4 Sampling Procedures and Tables for Inspection by Attributes, which we follow.
A defective is a unit of product which contains one or more defects. Defectives will usually be classified as follows:
Critical Defective: A critical defective contains one or more critical defects and may also contain major and or minor defect.
Major Defective: A major defective contains one or more major defects, and may also contain minor defects but contain on critical defect.
Minor Defective: A minor defective contain one or more minor defects, but contains no critical or major defect.
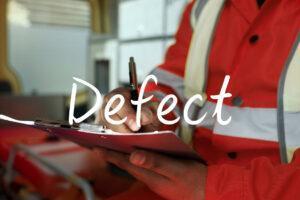
Randomness of the sample selected for inspection
To ensure a random sample is selected for inspection, we require that the lot must be formed for inspection. The presentation of the lot must be in the manner where each lot is to be presented and identified by a designated or approved responsible authority of the producer. As necessary, the producer must provide adequate and suitable storage space for each lot for proper identification and presentation, and personnel for all handling of product required for drawing of samples.
Random sampling technique can be supported by using the Random Number Tables and the following Random Sampling Procedures as presented in MIL-HDBK-53-1A Section 12.2.1.
Random Sampling Procedures
Each unit in the lot must be identified by a distinctly different number. For example, if there are 100 master cartons and each master carton contains 8 units of product. Each master carton is labelled in number from 001 to 100. Using the three-dimensional position of each unit (row, column, depth) and designate each unit as 1, 2, 3, … 6, 7, and 8 (clockwise counting from top-right as 1, and then 2, 3, and 4; clockwise counting from bottom right as 5, and then 6, 7, and 8).
Select random number from the Random Number Table. The corresponding unit selected for inspection can be according to the scheme, for example.
10480 >> 10-4-80 >> select from carton number 10 and unit 4 selected from the master carton.
22368 >> 22-3-68 >> select from carton number 22 and unit 3 selected from the master carton.
Note: For random number 77921 >> 77-9-21. Since there are 8 units in a master carton and there is no unit 9, this random number should therefore be skipped. The next random number 99562 >> 99-5-62 should be used. Therefore, the next selected unit should come from carton number 99 and unit 5 selected from the master carton.
The above number designation scheme is just one of many possible designations. Inspectors should create any scheme as appropriate to the specific lot quantity and master carton packing schema.
The first random number could be picked from the random number table, letting a pencil fall blindly at some number and start at that point. Toss a coin to decide which way to go: head goes up and tail goes down.
Appendix
Random Number Table
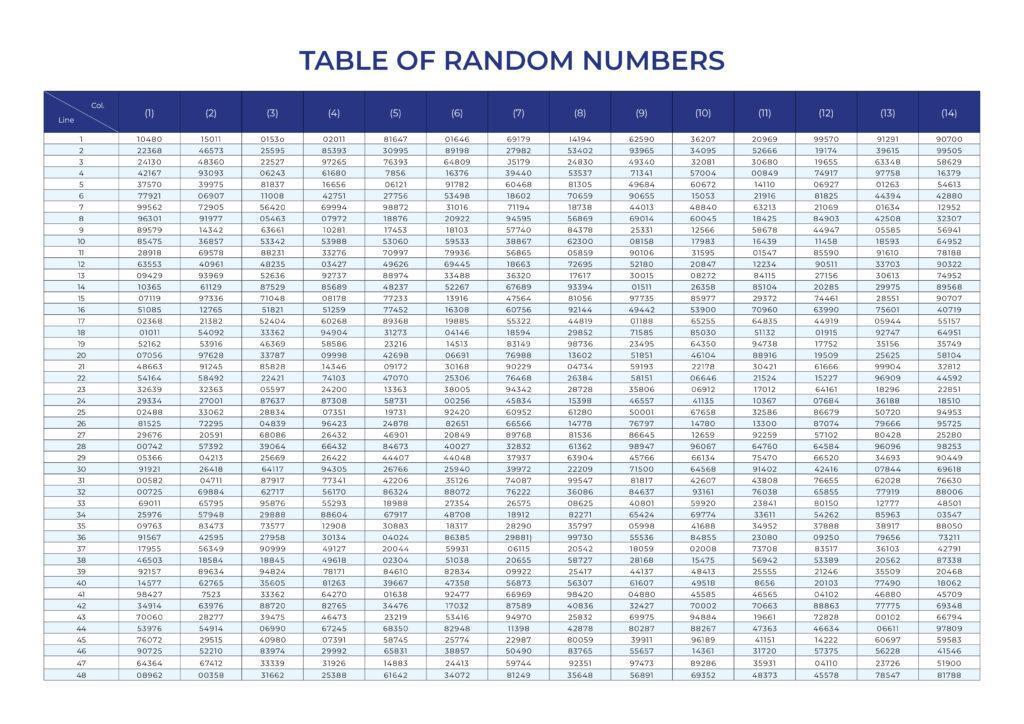