What is quality control?
To ensure that products meet quality requirements, you carry out quality control. Products of inadequate quality thus don’t end up on the market, with all the financial and operational consequences that this might otherwise entail. There are several different methods of quality control.
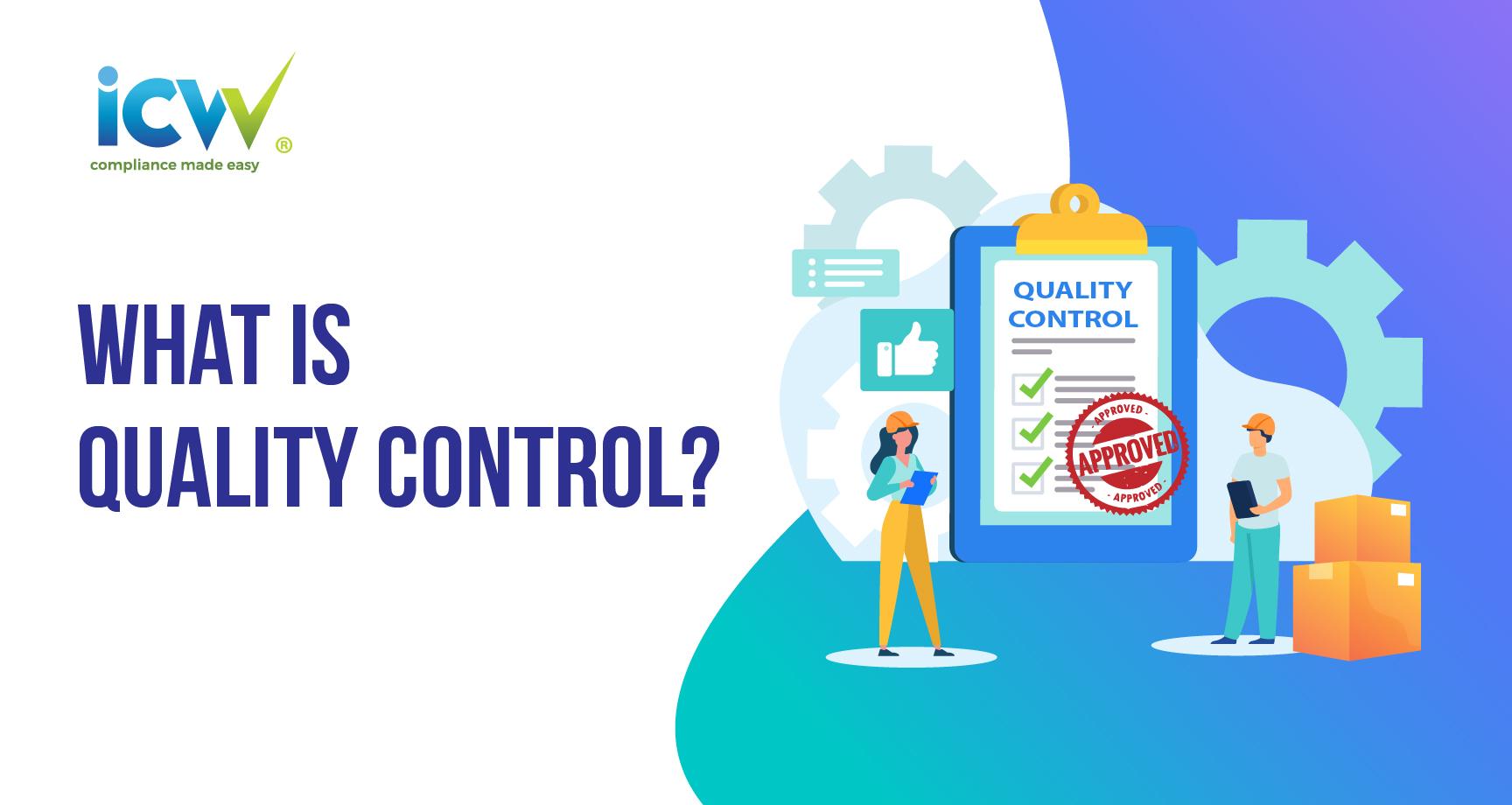
1. Quality control: meaning?
Quality control is all about checking products for quality and correctness.
Any workmanship faults are detected before shipping and can therefore be resolved at an early stage. As a result, the importer can always be assured that the shipped products meet quality requirements.
This is important because product quality can often be affected by deviations from target standards and by variability around target specifications.
Quality control can be carried out by first or second parties (buyers or sellers of the products concerned) or a third party (a testing, inspection and certification company such as SGS, Intertek, Eurofins or Underwriters Laboratories). The level of involvement of this third party depends heavily on the wishes of the buyers and sellers.
ICW offers a software platform which is specialized in compliance management. This platform is aimed at retailers, importers, brands and e-commerce platforms. The platform validates supplier quality and product compliance.
2. Why is quality control important?
The Hubble Telescope was launched in April 1990 to much fanfare.
Unfortunately, within weeks of its launch, it was determined that image quality from the Telescope was far below expectations. The blurry images produced were an embarrassment to NASA.
What was the problem?
It was later found that the primary mirror was ground too flat by… about 2200 nanometers.
In the end, tens of millions of dollars had to be spent correcting this mistake.
While your products probably won’t need to be so precisely made, it is obvious from this story that even small mistakes in production that cause product quality to fall short of customer expectations can be damaging, both monetarily and reputation-wise.
Some additional benefits of quality control:
Ø Dangers can be identified promptly to prevent recalls.
Ø Problems can be identified before products need to be discarded.
Ø Production methods can be streamlined to improve efficiency and save costs.
Ø Strict regulations can be enforced based on QC to ensure consistently high quality.
Ø Improved worker morale. No one wants to be associated with the production of inferior products!
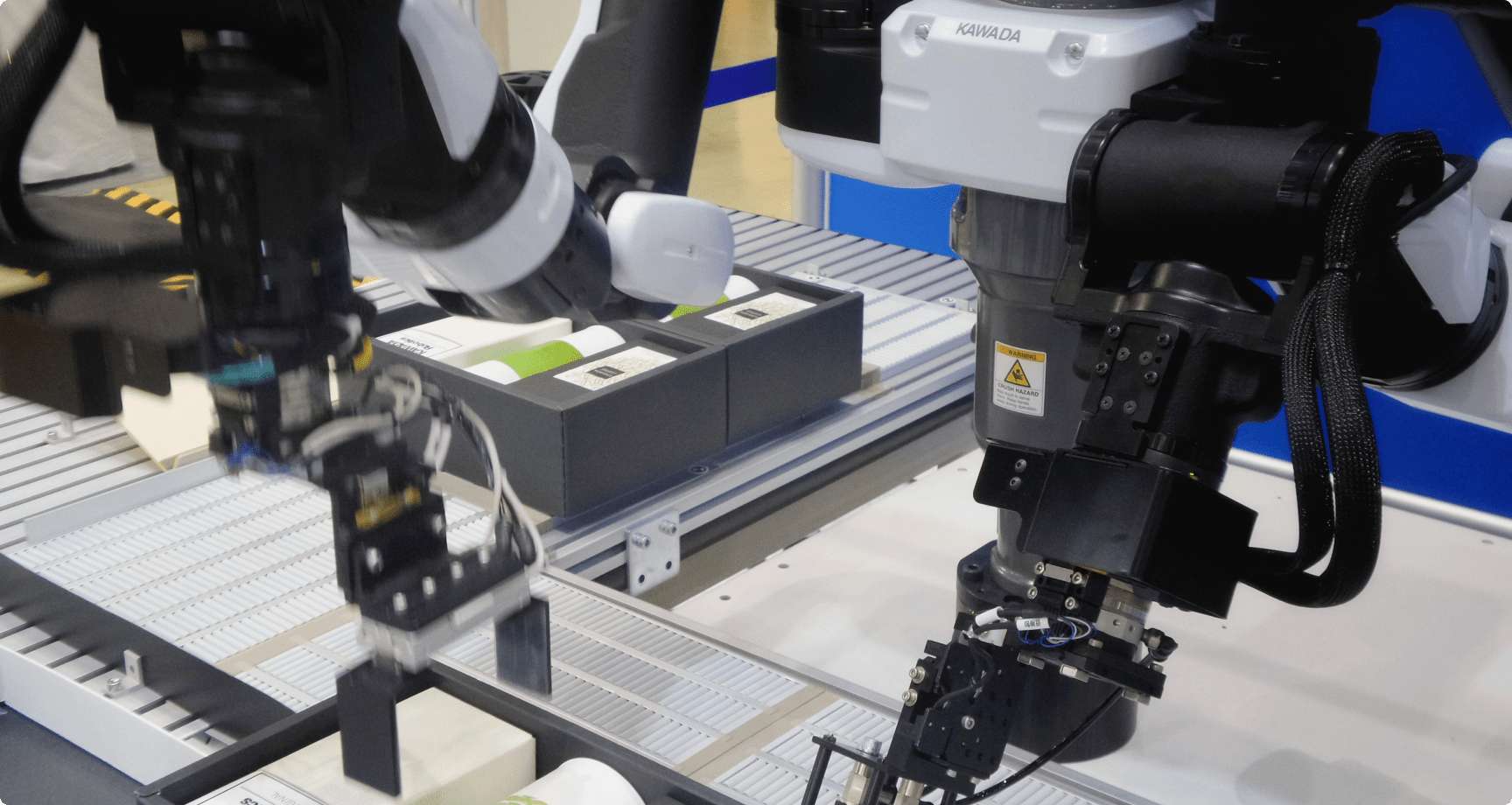
3. How quality control is done
In all quality control inspections, the sample size taken for testing should be representative of the total products produced and be according to AQL requirements.
A quality control inspection is usually performed using the concepts of acceptance quality limits (AQL) as well as AQL sample sizes as described in the ISO 2589-1 or its equivalent standards, MIL-STD-105e, ANSI/ASQC Z1.4-2003, NF06-022, BS6001, DIN40080, and GB2828.
There are generally three types of inspection carried out at different stages of production. They are the pre-production inspection or initial production inspection (PPI or IPC), during production inspection (DPI or DUPRO) and the pre-shipment inspection (PSI).
A. Quality control: Acceptance quality limits (AQL)
This is described as “the lowest level of quality that is still acceptable”.
For example, “AQL is 1%” means “On average, I want no more than 1% of my items to be defective in the whole order quantity over several production runs with this supplier”.
Usually, defects found are categorized into three different groups: minor, major and critical defects.
Take a shirt as an example.
A minor defect may be an untrimmed thread, which can be easily fixed.
A major defect may be missing stitches, which can affect the appearance of the shirt or even seam strength.
A critical defect would be a needle found in the shirt, which could cause an injury.
Different AQL limits are to be set for each of these three categories. Obviously, you will have the lowest tolerance for critical defects and thus the AQL limits for these will be the lowest.
How high or low you set these limits will depend on several factors, such as your market, consumer preferences or the level of risk involved for your end-user (airplanes or drugs for example can’t have many or even any defects, which could otherwise lead to injuries or at the worst loss of life).
B. Quality control: AQL sample sizes
The sample size for testing as specified in ISO 2589-1 is determined based on inspection level and lot/production size.
So, what is an inspection level?
Inspection levels are just that: the “level” of inspection you want. They are grouped into three general categories, General Inspection Levels I, II and III.
Level I involves the smallest sample size and is your best bet if you are short on time and/or money. Level II is considered “normal” and is the most commonly chosen option. Level III involves the largest sample size and offers the greatest assurance of order status and quality.
For example, if you have a 5,000-piece lot size, Level I will involve plucking 80 units out for testing, Level II would take 200 units and Level III would take 315 units.
Levels I, II and III will be different for a lot size of 20,000 pieces.
You may consider using a Level III inspection if:
Ø Your supplier has a history of producing poor quality goods.
Ø This is your first order with the supplier.
Ø This is your first order of a newly developed product.
Ø The product is of particularly high value (e.g., luxury watches) or poses particularly high risks (e.g., medical devices).
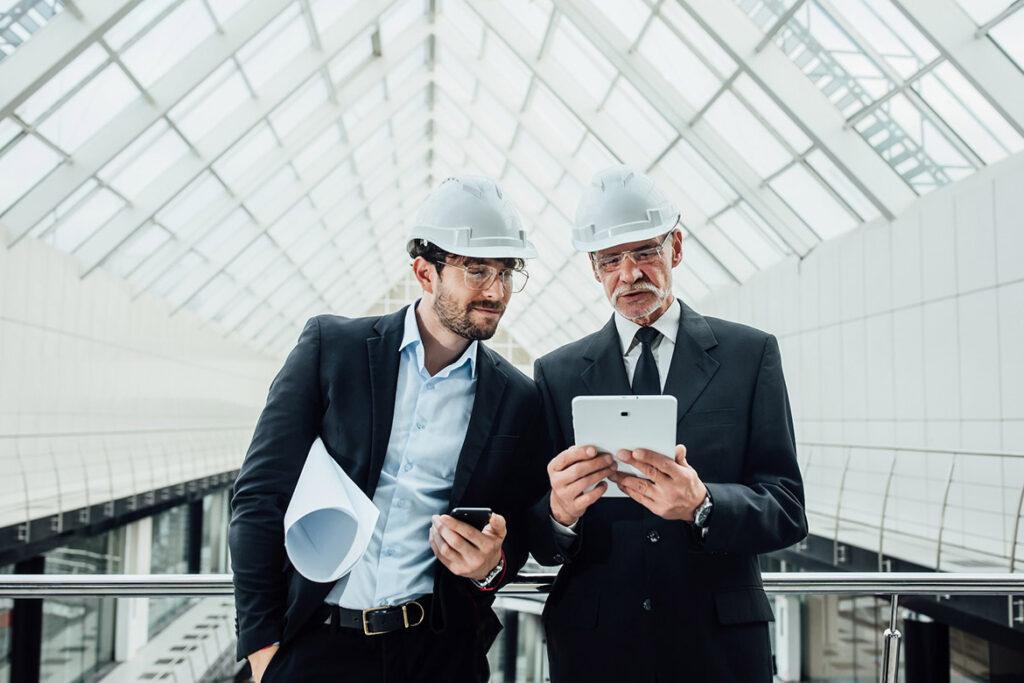
So to summaize, quality control is usually done according to the acceptance quality limit( AQL) and AQL sample sizes as described in ISO 2589-1 or its equivalents. Limits for the maximum number of defective goods are determined by you and depend on many factors. Different limits should be set for minor, major and critical defects. Sample sizes are based on the inspection level (General Inspection Levels I, II, III) you want or need product size.
Such parameters are set for each of the different methods of quality control carried out, as explained in the next section.
C. Quality control method: Pre-production inspection
During the pre-production inspection, the third-party inspector inspects the raw materials which the manufacturer will use to produce the end product.
The PPI can also cover semi-finished products for which production has started but are not finished yet.
A PPI is beneficial whenever you work with a new supplier, especially if the project is a large one with critical delivery dates. It is also important when you suspect your supplier has sought to cut costs by substituting cheaper materials before production.
Furthermore, the PPI can reduce communication issues between you and your supplier regarding shipping dates, production timelines, quality expectations and so on.
Ø A good understanding of production schedules.
Ø The ability to anticipate potential issues that could affect project timing or product quality.
Ø Assurance that your requirements will be fulfilled.
Ø Assurance regarding raw material quality and product components.
D. Quality control method: During-production inspection
During the during-production inspection (DPI or DUPRO) the third-party inspector inspects a prescribed amount of the finished products after 15% – 70% of the products are completed. This percentage depends on the order quantity and risk level of the product and manufacturer.
The inspector checks the products on appearance, functionality, color, packaging, quantity and so on.
Defects found during the DPI may be noted in a corrective action plan (CAP) and corrective actions can be taken with minimal disruption to production, which therefore leaves the manufacturer with a bit of wiggling room.
DPIs can be done as a follow-up when problems with quality are found during a pre-production inspection. Problematic batches found during this PPI will be re-checked for defects during the DPI to confirm such problems have been fixed.
If the inspector finds a defect rate higher than the required AQL limits the inspection will be reported as FAILED, if the defect rate falls within the required AQL limits the inspection will be reported as PASSED.
The advantages of doing a DPI include:
Ø Quality and compliance to specifications is maintained throughout the production process.
Ø Any issues can be detected at an early stage and corrected promptly.
E. Quality control method: Pre-shipment inspection
The most common method of quality control is the pre-shipment inspection (PSI).
During this pre-shipment inspection, units are randomly selected from all batches of your order. This is done when production has been completed to a certain percentage.
During the pre-shipment inspection (PSI) the third-party inspector inspects a prescribed amount of the finished products before they’re loaded onto the container.
The inspector again checks the products on appearance, functionality, color, packaging and quantity, etc. The inspector notes down all of his or her findings and publishes an inspection report.
This inspection generally takes place at the manufacturer’s premises or the harbor.
As is the case with a DPI, If the inspector finds a defect rate higher than the required AQL limits during the PPI the inspection will be reported as FAILED, and if the defect rate falls within the required AQL limits the inspection will be reported as PASSED.
According to SGS — one of our partners — A pre-shipment inspection:
Ø Assures you of the quality, quantity, marking, packing and loading of your shipments;
Ø Helps you ascertain that your goods are handled safely and correctly;
Ø Helps you ensure that your goods arrive at their place of destination in compliance with technical specifications, quality standards and contractual agreements.
F. How quality control can be done more effectively
Many companies still use paper for their audit processes, but this makes it difficult to do follow-ups and glean insights from the information collected.
Digital records are thus an advantage.
Digitalization also boosts standardization. Products that are produced simultaneously in different factories still need to be identical when they reach retail, and the risk of accidental variations is higher without standardization and proper quality management.
A cloud-based quality management system keeps all parties on the same page with centralized information such as audit results that are accessible to everyone involved.
Furthermore, it is next to impossible for a sourcing executive to make decisions purely on gut instinct, with all the elements involved in the supply chain.
There is an increasing need for companies to transition from subjective to objective decision-making which means outsourcing some activities to AI.
People, of course, still have a place in strategic planning, but by leveraging cloud-based compliance management software, executives can save time and come to better informed, KPI-driven conclusions.
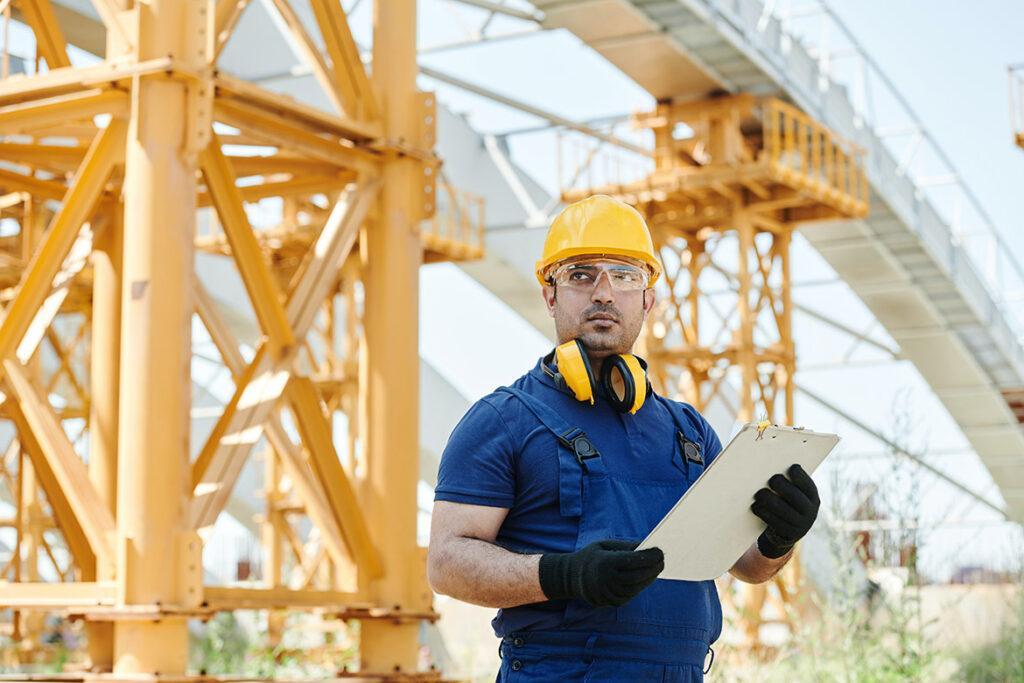
G. What does ICW do?
We provide intelligent compliance management and a certification marketplace for buyers, sellers and assigned third parties to manage quality control and the compliance chain of suppliers and their products.
ICW’s QMAS is a CMS that lets you store and manage your compliance documents, as well as alerts you when audit certificates and testing reports are about to expire.
The data we give you can also be analyzed for supplier performance and help you make decisions on TIC spending.
Furthermore, for companies wanting to source from Asian manufacturers, we have a platform that provides comprehensive information on suppliers who have been validated for various quality control standards.
ICW’s i-Source Supplier Profile Database provides over 100,000 supplier profiles, allowing you to compare and contrast between vendors of appliances, textiles, toys and more.
What sets our database apart from the competition is the fact that apart from more typical supplier information — ranging from product allocation to line and monthly capacities — we also include information about compliance with quality control standards such as Sedex, BSCI, BEPI, ISO 9000 and ISO 14000.
At ICW — a service used by the world’s largest pharmaceutical, healthcare and beauty chain store, the largest importer in Europe, top global toy distributors as well as thousands of brand manufacturers — we ensure your quality control processes are done properly.